Leak Testing
A leak corresponds to the passage of a fluid or a gas for example, through a crack of a certain thickness in a wall.
This crack is usually complex, it does not follow a straight line and can have an evolutionary width between its beginning on one side and its end on the other.
A leak cannot technically exist if there is no pressure difference on either side of the “cracked” wall. This pressure can be the weight of a static liquid or the pressure of a compressed gas in need of escaping into the atmosphere, always from the area of higher pressure to the area of lower pressure.
To quantify a leak, we talk about its leakage flow, defined by the following formula:

It is therefore possible to calculate acceptable leakage flows, also called release threshold in the case of a test over a given period of time associated to an acceptable loss.
A gas leak testing system using Helium gas, H2 gas, … includes, among other things:
- A tracer gas: both helium and hydrogen are used. Pure Helium can be used for more sensitivity or can be diluted for economic reasons. Hydrogen can only be used as a tracer in a diluted form, typically in nitrogen, up to 5% (5% H2 95% N2). Hydrogen will be limited to sniffing testing in the atmosphere (see below), for the reason that many materials release hydrogen under vacuum, thus interfering the measure.
- A leak detector: an essential mass spectrometer working under vacuum. The analysis cell is calibrated to detect and precisely quantify the helium or the hydrogen escaping from the tested products.
- Vacuum pumps or groups of vacuum pumps: whether it is for a vacuum test or for a sniffing test, the products to be tested will be evacuated using a primary pump before pressurizing them. Similarly, the vacuum chamber as part of a global test (see below) will have to be evacuated up to 10-2 or 10-3 for example, for a sensitivity of the order of 10-6atm.cm3/s.
- A frame: according to your requirements, it is composed of a mechanically welded frame of polycarbonate protective panels and aluminum profiles. It also supports other components such as vacuum pump groups, electrical cabinets, etc.
An Operator Interface for an optimal management of the system: a touch screen to control the machine’s automation, an additional flat screen to check the curves of the testing cycle (pressure, testing time, etc.), a LED light column for use in production… All configurations are possible.
Global Test
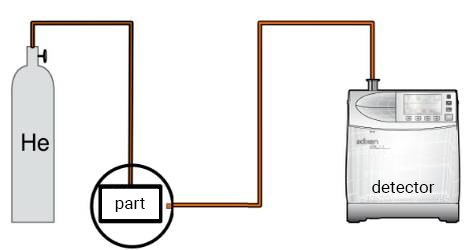
- The part is placed in a vacuum chamber
- The detector is connected to the chamber
- The chamber is evacuated
- The part is emptied from its air and then pressurized with helium
- The helium escapes from the chamber and is quantified by the detector.
Sniffing Test
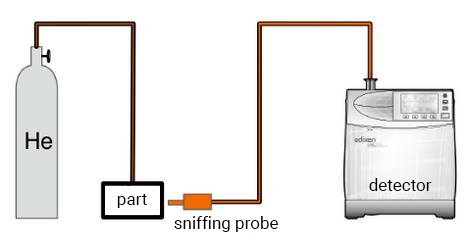
- No vacuum chamber is required
- The part is pressurized with helium
- The sniffing probe is connected to the leak detector
- An operator goes through and around the chamber until leak detection.
Aspersion Test
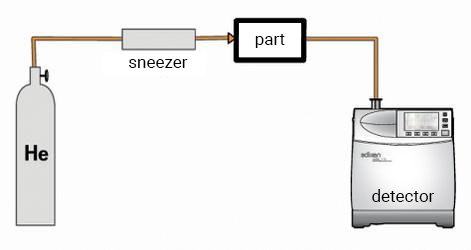
- The part is pumped by the detector itself or by a parallel pump
- The detector is therefore connected to the part to be tested
- The operator blows helium into the areas that may contain leaks
- The helium enters through the crack and is quantified by the possible detector.